There are five major commodities mined in WA that have substantial downstream processing. Credit for most of the value adding can be attributed to investment decisions taken decades ago, as Mark Beyer reports.

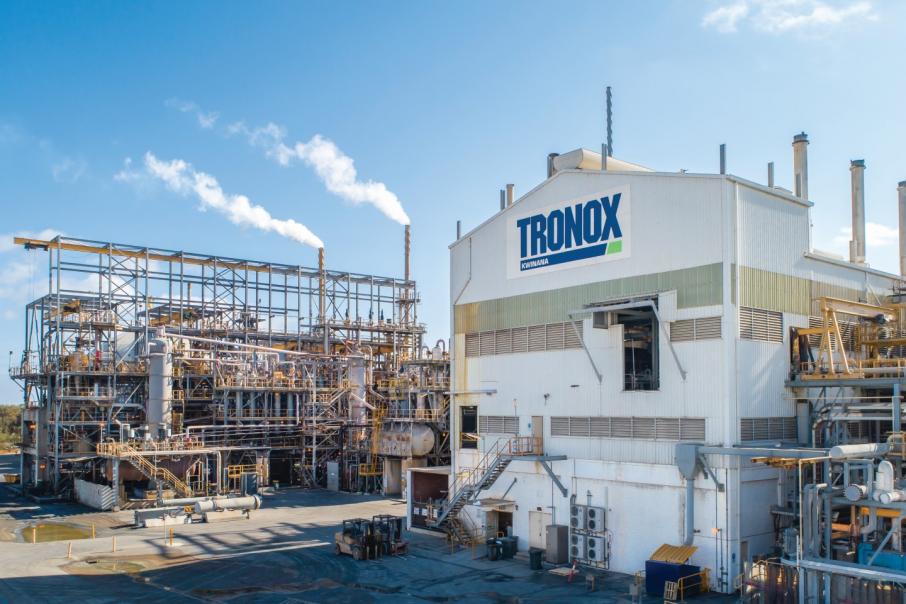
There are five major commodities mined in WA that have substantial downstream processing. Credit for most of the value adding can be attributed to investment decisions taken decades ago, as Mark Beyer reports.
(click here to view a PDF version of the 12-page liftout)
Gold – 1890s
The Perth Mint was established in 1899, just a few years after the discovery of gold in Kalgoorlie triggered a mining boom that transformed Western Australia.
It was Australia’s third branch of Britain’s Royal Mint, the others being in Sydney and Melbourne.
While they have closed, the Perth Mint has become the producer of Australia’s official bullion coin program and a substantial player in the global gold market servicing miners, investors and collectors.
Still operating from its original location in East Perth, the mint had sales of close to $18 billion last financial year.
The simplest and best measure of its value adding capacity is its trading profit, which was $96 million.
That’s the difference between the cost of gold it buys from miners and the price at which it sells the end product after its value adding activities.
As the world’s largest refiner of newly mined gold, Perth Mint refines almost all of Australia’s gold production and a substantial amount mined overseas.
The unrefined gold ‘dore’ delivered to the mint can be anywhere from 60 per cent to 95 per cent gold.
The mint refines this material to a minimum 99.5 per cent gold so it can be traded on the major exchanges around the world.
It also produces gold bars, coins and other minted products with 99.99 per cent gold.
“That’s really where the value adding starts,” general manager refining Nathan Edwards said.
The bullion bars are sold into overseas markets, mostly in Asia but also the US.
Perth Mint produces and markets about 8 million gold and silver coins each year.
One of the biggest markets for these precious metal coins is Germany; in fact, the Perth Mint is Australia’s largest exporter by value to Germany.
The Perth Mint is also the ‘Fort Knox’ of the Southern Hemisphere, with about 37,000 investors from 130 countries using its deposit services.
Mineral Sands – 1950s
When people drive from Perth to the beaches at Busselton or the wineries at Margaret River, most would be oblivious to the substantial mining operations they have passed in the South West.
The mining of mineral sands began near Busselton and Capel in the 1950s and continues to the present day.
New York-based Tronox and Perth-based Iluka Resources, which dominate the industry, have since expanded to new mines in the Mid West, as well as interstate and overseas.
More significantly, they have extensive processing operations in the South West.
Unlike smaller miners that sell heavy mineral concentrate to third-party processors, often in China, Tronox and Iluka capture much of the value add in Australia before selling refined products to overseas manufacturers of paint, ceramics and plastics.
Iluka’s major facilities include the Narngulu plant near Geraldton, one of the largest of its kind in the world, where it produces zircon, rutile and ilmenite.
It conducts further processing at Capel, where the ilmenite is upgraded to synthetic rutile. This increases the titanium component of ilmenite from 50-60 per cent to more than 90 per cent.
Similarly, Tronox produces zircon, ilmenite, leucoxene and synthetic rutile at its Chandala plant, just off the Brand Highway at Muchea.
Tronox goes a step further, converting its synthetic rutile into titanium dioxide at pigment plants at Kwinana, Kemerton and Australind.
Its Western Australian operations form the world’s largest integrated titanium dioxide project.
They also have a long history, with the Bunbury operations commencing in 1961.
Together, the two companies employ about 1,500 people across their WA operations.
Alumina – 1960s
Alcoa of Australia and Worsley Alumina are two of the biggest employers in Western Australia’s South West, thanks to investment decisions made decades ago.
Both Alcoa and Worsley run integrated operations that encompass bauxite mining and alumina refineries.
The mining and refining are co-dependent – they would not exist without the other.
The extensive bauxite deposits in the Darling Range are low in grade but they are easy to mine and close to the refineries, which in turn have good access to power supplies, ports and skilled labour.
Development of Alcoa’s WA operations began in 1961, and its Kwinana refinery came on stream in 1963.
That was followed by refineries at Pinjarra in 1972 and Wagerup in 1984, supported by two bauxite mines.
Collectively, these operations employ about 4,000 people.
South32 subsidiary Worsley Alumina operates further south, with its bauxite mine near Boddington and an overland conveyor taking the ore 50 kilometres to the refinery at Collie.
Its operation started in 1984 and capacity has been increased four-fold since then, employing 2,000 staff and contractors.
There has occasionally been talk of WA taking the next step in value adding, with construction of an aluminium smelter.
However, most aluminium smelters around the world use subsidised power, and consequently their economic value has been hotly debated.
A case in point is Alcoa’s smelter at Portland in Victoria, which faces an uncertain future as its power supply is renegotiated.
Nickel – 1970s
Nickel production emerged rapidly in the 1970s to become a substantial part of Western Australia’s resources sector, and most of its downstream processing facilities date from that time.
The sector has several major producers, including Western Areas, IGO, and Glencore; but the big player, especially from a value add perspective, is BHP Nickel West.
Nickel West is a vertically integrated business with more than 3,500 employees and contractors.
On the brink of closure a few years ago, it’s now on a growth path as it seeks to take advantage of increasing demand for battery metals.
Nickel West operates several mines and concentrators in the Goldfields, including at Mt Keith, Leinster and Kambalda, and processes ore from its own mines as well as ore from third parties.
The concentrate is sent to its Kalgoorlie smelter, which uses a flash furnace to produce granulated nickel matte.
Next step is Nickel West’s Kwinana refinery, which turns the matte into premium-grade powder and briquettes containing 99.8 per cent nickel.
More than three quarters of BHP’s nickel is sold to global battery material suppliers.
Two years ago, Nickel West committed to move further up the value chain by building a nickel sulphate plant at Kwinana.
Stage one is expected to produce up to 100 kilotonnes per annum of nickel sulphate, a product used in the lithium-ion batteries that power electric vehicles.
Ammonia – 2000s
The Burrup Peninsula has long been touted as a downstream processing hub, ideally placed to take advantage of the abundant gas production in Western Australia’s north-west.
Despite the high hopes, there is only one established value adding facility on the Burrup.
Norwegian fertiliser giant Yara International owns an ammonia plant that was originally developed by Pankaj Oswal’s Burrup Fertilisers.
It is one of the world’s largest ammonia plants, but as a highly capital-intensive facility is not a big employer, with only about 190 workers.
Yara Pilbara has also teamed up with explosives manufacturer Orica to build a $US800 million technical ammonium nitrate (TAN) plant next to its existing facility, to further process the ammonia.
Construction of the TAN plant was completed in 2016 and at its official opening, then premier Colin Barnett said its output would be up to 10 or 12 times that of the raw material inputs.
However, like many projects in the Pilbara, there were major problems during construction and commissioning, with Yara and Orica needing to make big investments in rectification works over the next three years.
In its most recent update, in May this year, Orica said the plant was finally operational and ramping-up to commercial levels this calendar year.
The TAN plant will compete with other producers of ammonium nitrate, including Wesfarmers CSBP, which operates a processing plant at Kwinana.
Despite this setback, Yara is pursuing a new opportunity on the Burrup.
It has teamed up with energy company ENGIE to assess the development of a solar powered hydrogen plant that would allow it to produce ‘green’ ammonia.