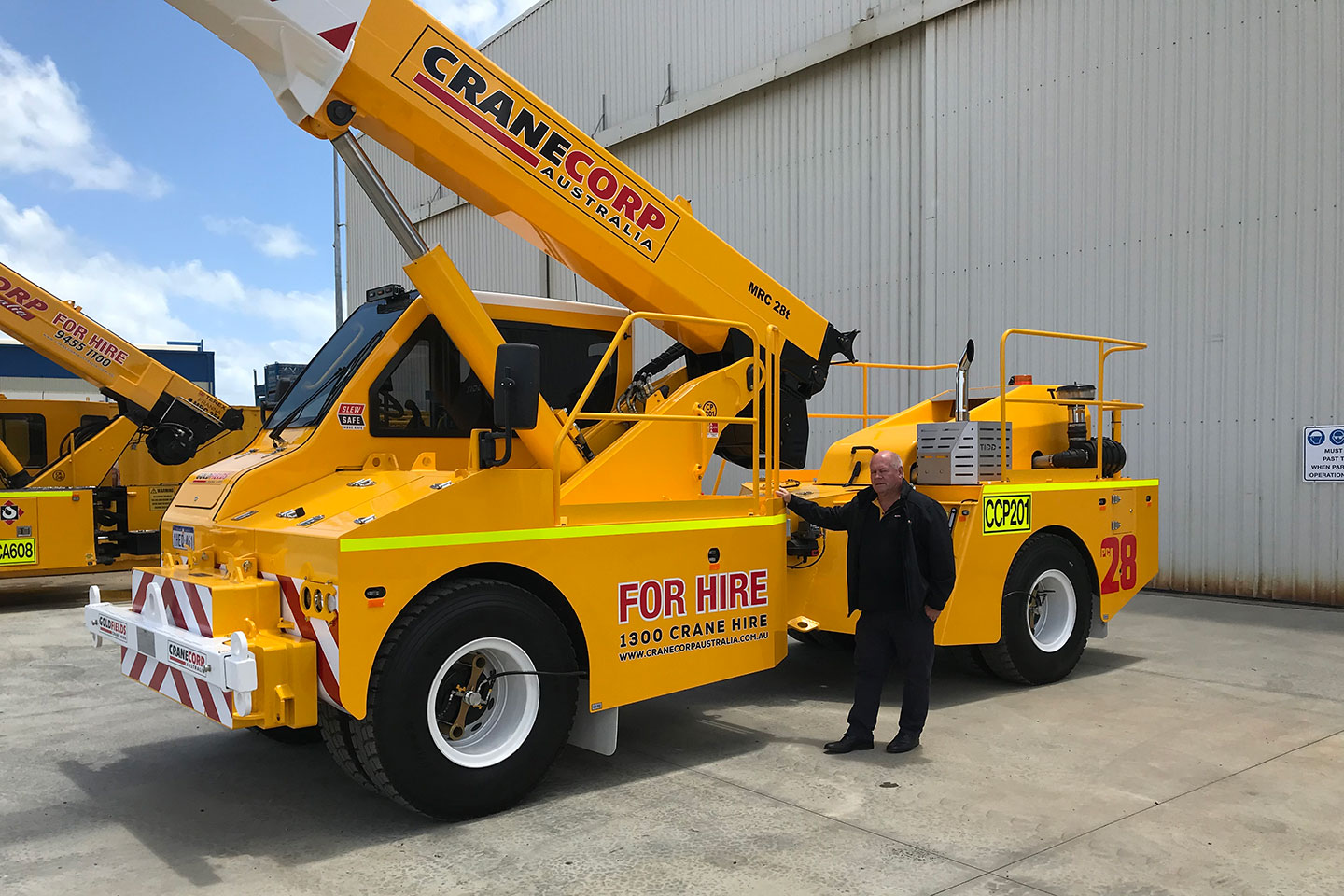
The mammoth task of lifting a $30 million dollar helicopter into a city skyscraper isn’t exactly business as usual but it is a very real example of the challenges, risks and complexities the crane industry faces every day.
The dramatic lift was needed to install the centrepiece for a major resource industry conference and trade show, but it could just as easily have been swinging millions of dollars of precision engineering off a cargo ship, or lining up three cranes to install track switches over 100 kilometres of remote outback railway line.
Picking things up and putting them down has become a demanding science and, like many other progressive businesses, Western Australian crane industry leader Cranecorp Australia, is using digital transformation to its advantage.
As WA’s mining industry continues to press ahead, with investment in new mines, expansions and refurbishment encouraged by strong commodity prices, Cranecorp is using technology to reduce the cost and risk of complex lifts, for itself and its customers.
Cranecorp CEO Rod White said, “Traditionally, the crane industry has been slow to change, relying on buying bigger cranes to do bigger lifts. There are many self-made owner operators in the industry, and it is part of their culture to stick with the tried and true.
“But that thinking is changing and the industry is becoming more sophisticated and benefitting from the digital transformation happening around us.
“Cranecorp has specialised in the mining and heavy industrial sector for more than 20 years. Like other parts of the mining industry, we are using tools like data-based decision making and automation, not just for productivity, but to protect the safety of our people and equipment.”
Pre-job planning has become a key aspect, combining years of operator experience with advanced engineering modelling to ensure the tactics for each lift are clear and the right people and equipment are available.
Computerised load control, using advanced geospatial positioning, is moving riggers away from the danger of swinging loads and allowing crane operators to manoeuvre in confined spaces with greater precision.
Safety for people and plant is one of our key drivers and technology is being used to engineer out many traditional risks, according to Cranecorp’s General Manager of Operations Adrian Third.
“Clients often think a bigger crane is better. Ordering a crane that is bigger than you need can have a big impact on the budget. For example, it is not efficient to use a 300T crawler crane if a 250T all-terrain crane can do the lift at a significantly reduced cost. The smaller and more agile crane also gives you the opportunity to easily do additional lifts on site if required. A big crawler moves at less than one kilometre an hour, so moving it between short jobs isn’t viable. Expert, professional lift planning takes the educated guesswork out of the process and gives clients the data and the confidence to known when a smaller crane can do the job,” he said.
“When it comes to choosing cranes to undertake work, price is an important factor for our clients. The lowest rate offered is not the sole factor to be considered in assessing a quote. There are many other factors to consider including selecting the optimum crane for the lift. Technology and the experience of operators and riggers can save considerable time in completing a job providing significant time savings well in excess of any difference in hourly rate. We also avoid the many add on extras that many companies choose to surprise their clients with when the final invoice arrives. All these factors can contribute to a lower overall cost when it comes to managing the total project cost,” said Adrian.
GPS is becoming an increasingly important technology with many of the newest cranes fitted with advanced systems for handling precision lifts where there is very little margin for movement. Additionally the heavy vehicle transport system feeds data into the daily driver log which is vital for tracking a vehicle’s location in remote areas, with geofencing capable of guiding the driver to roads that are capable of handling big vehicles providing greater peace of mind for operators.
“Tyre degradation is a great example of where technology can assist in managing what can potentially be a big problem if not managed well, particularly in the extreme heat of WA’s Northwest and Goldfields. “Damage from a blown tyre could take a crane out of operation for a month and that quickly adds up to hundreds of thousands in costs and lost productivity and customer dissatisfaction so we do everything we can to prevent tyre failures. With more than 200 fleet assets, and up to 14 tyres on the bigger cranes each worth around $2,500 each, Cranecorp has millions of dollars in rubber on the road at any time”.
“We are working with providers on a computer controlled tyre management system that feeds into our GPS systems allowing us to track tyre condition live, giving us time to react to any changes and significantly prolong tyre life by doing things like automatically reducing vehicle speeds or if required stopping to manage tyre temperature.”
The Traction Air™ system available with the Tidd cranes is a step forward in improving tyre life risk management. Cranecorp has recently taken delivery of the first of six new TIDD PC28 pick and carry cranes adding to the substantial fleet it operates across WA, particularly in the mining centres of the Northwest, Goldfields, Mid-West, and South-West/Metro. The TIDD PC28 are constructed using the highest quality components, and prioritises safety throughout its design, with advantages such as Slew Safe™ and Traction Air™ which combine to ensure that the crane is always operated at the optimal tyre pressure and with the limits of its charts, thus ensuring the tyres on the assets are at the correct operating pressures regardless of the external environment automatically adjusting for the heat and the cold and improving the safety of the crane for the operators.
For more information visit www.cranecorpaustralia.com.au or call 1300 CRANE HIRE