Globe Metals & Mining has achieved metals extraction of more than 99 per cent on concentrates from its Kanyika niobium project in Malawi following a savvy decision to switch to vapour-chlorination technology. The company says the results validate its decision to move from high-cost, toxic, acid-based extraction and also highlight many other cost, processing, infrastructure, environmental, handling and ESG benefits.
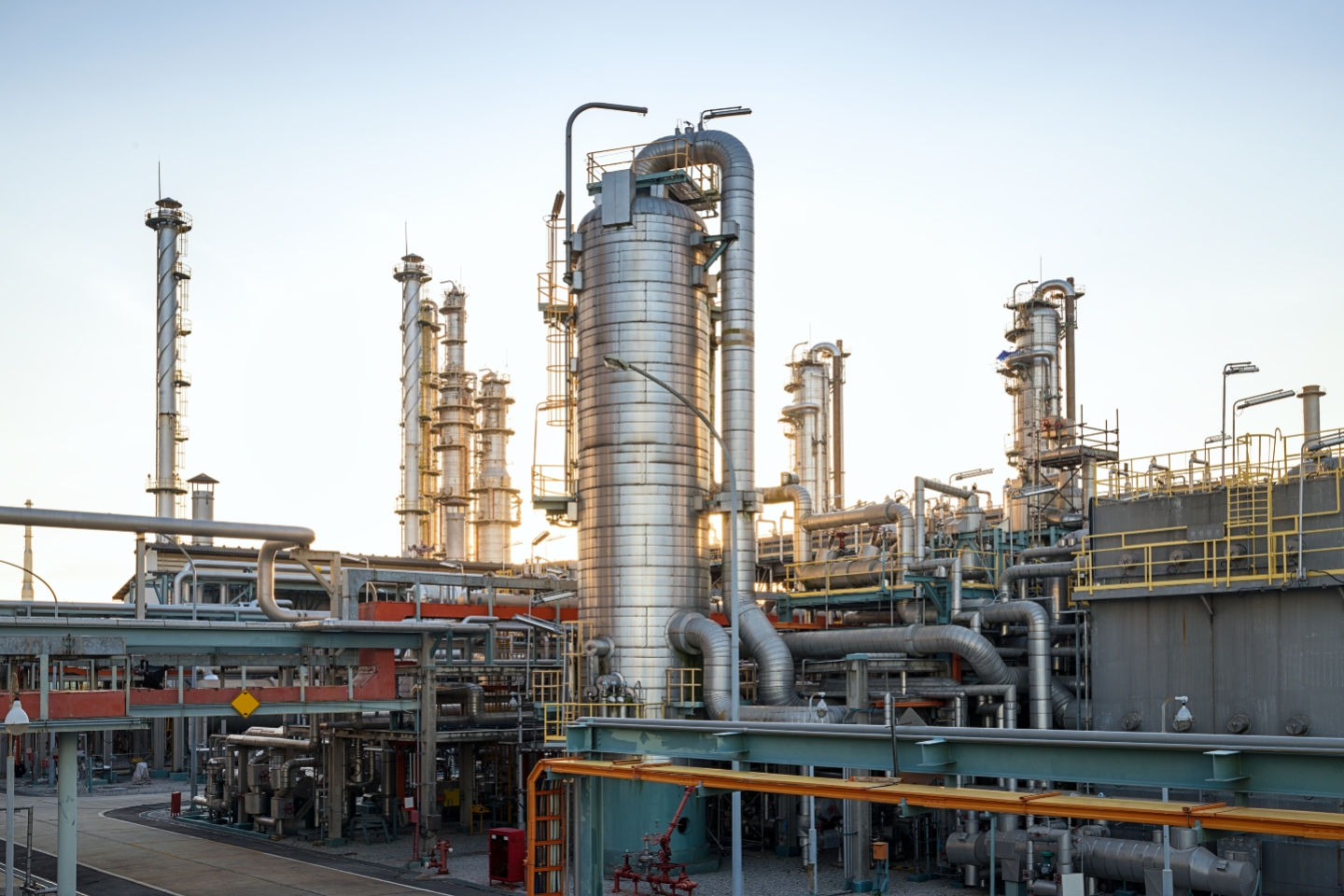
Globe Metals & Mining has achieved metals extraction of more than 99 per cent on niobium and tantalum concentrates from its Kanyika project in Malawi following a savvy decision to switch to vapour-chlorination technology.
Management says the results from testwork carried out by metallurgical consultants TCM Research validate its decision to move from high-cost, toxic, acid-based extraction and also highlight many other cost, processing, infrastructure, environmental, handling and ESG benefits. The chlorine is regenerated and recycled during the process.
Globe says that when initial baseline testwork yielded extraction rates of 98 per cent for niobium and 90 per cent for tantalum, it was prompted to conduct a further series of kinetic and optimisation tests, which culminated with extraction rates exceeding 99 per cent for both metals. The testwork also demonstrated high yields for other potentially marketable products, including titanium and zirconium, with extraction rates of more than 99 per cent and 96 per cent, respectively.
With one test yielding extraction rates for niobium of 99.9 per cent, tantalum 99.8 per cent, titanium 99.9 per cent and zirconium 95.9 per cent, the company’s engineers expect that overall recoveries across its planned refinery will be about 99 per cent. The company says that compares favourably to the 95 per cent recovery rate based on the hydrofluoric acid extraction process envisaged in its feasibility study in August, 2021.
Globe Metals & Mining chief executive officer Grant Hudson said: “An extraction of >99% is a marvellous result as we continue to maximise the efficiencies of our various processes, and will have a direct, positive and project-long effect on our profitability. Combined with its superior ESG profile these outcomes continue to validate our decision to switch to chlorination technology in our refinery and I look forward to positive results from the next stage of testwork.”
TCM is conducting the metallurgical testwork using its proprietary vapour-extraction process on a concentrate sample from Globe’s Malawi project. It has developed a suite of vapour metallurgy processing technologies for the treatment of a range of materials from which metals including niobium, tantalum, iron, titanium, vanadium, tin, tungsten and rare earths may be extracted.
Globe envisages that its partners, offtakers and future buyers will expect a more environmentally-sustainable niobium oxide supply. It believes TCM’s process meets that requirement and has advanced the metallurgical testwork to separation and refining stages.
The process offers the ability to produce a range of high-value products for a diverse and growing range of industries, with increased benefit along the supply and value chain. Globe says its aim is to bridge the gap between the mining and manufacturing industries to reduce the overall environmental impact.
The company says TCM’s vapour process, particularly in relation to niobium and tantalum concentrates, offers the opportunity to produce additional co-products from other constituents such as titanium, zircon, and iron, in addition to the potential to recover any rare earths present. It says the extraction process employs a selective vapour reductive chlorination technique, where the target metals are volatilised and removed from the host matrix.
At the base of the process is the formation of metal chlorides with differing melting and boiling point temperatures, which enables downstream processing such as further separation and purification to produce individual metals or compounds. The second stage of the process involves the refining and production of saleable products employing metal chlorides that can be separated and refined via dry vapour metallurgical techniques, fractional condensation, de-sublimation, fractional distillation, chemical vapour transport and halide substitution.
The separation and refining stages provide for a final stage of product differentiation, enabling the production of a range of saleable mixtures, compounds or individual metals or their alloys or powders
Globe recently signed a non-binding term sheet with TCM, giving it exclusive use of that company’s technology for the extraction of niobium from the Kanyika project.
It has also commissioned TCM to design the refining process and refinery infrastructure for the Kanyika concentrates, including metallurgical testwork and the establishment of a pilot plant to demonstrate the viability of extraction and the refining of high-grade niobium, tantalum and other metals from the project.
Is your ASX-listed company doing something interesting? Contact: matt.birney@businessnews.com.au