
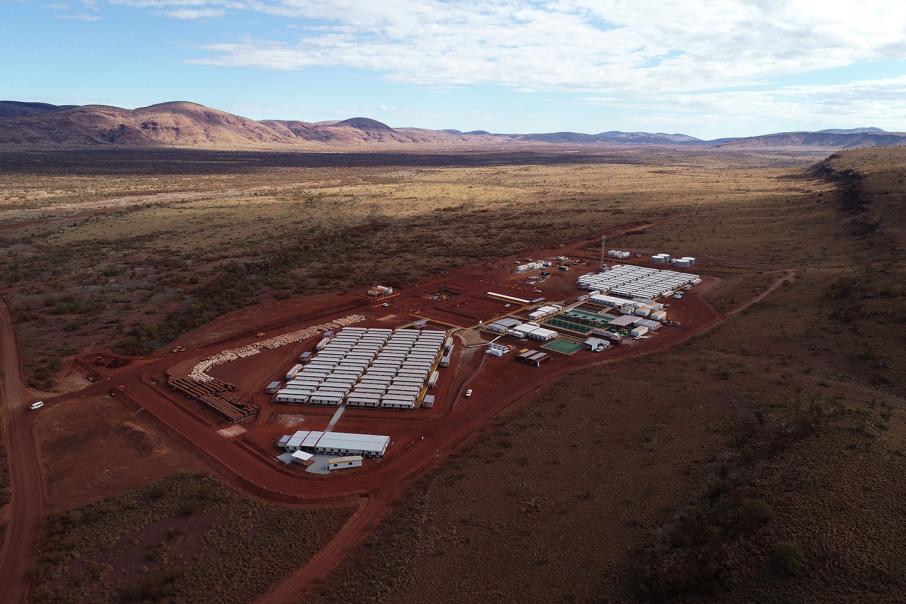
Mining is synonymous with Western Australia and ATCO’s name is synonymous with mining camps as the company manufactures the temporary buildings affectionately referred to as ‘dongas’, that house thousands of mine workers right across the state.
Most of those are modular construction, fabricated in ATCO’s 14,000 sqm facility in the Latitude 32 Industrial Zone in Kwinana. It is the largest, custom built modular manufacturing facility in WA and ATCO's largest modular manufacturing operation in Australia.
According to managing director Tom Parojus the site was chosen for its easy access to distribution networks including road, rail and the port and enables it to draw on established supply chain infrastructure and workforce for the future growth of the business.
“People were surprised when we built this new facility when the mining boom ended, “he says.
“But mining goes in cycles and we built this to have a business in WA for the long term, not to cash in on the boom and leave. What we do here, we couldn’t do if we didn’t have such a state-of the-art facility.”
So, why does modular construction work better in WA than in-situ-construction work?
Group general manager Western Australia Brad Tucker says where housing needs to be produced quickly, in high volumes and to a repetitive design, building in a quality-controlled facility and transporting modules to site is by far the most cost effective way. This is particularly the case where the buildings are needed in a remote location and the logistics of building in-situ are difficult because of sheer remoteness, harsh environments and as a result is very expensive.
“If you need construction in the remote Pilbara, modules will be a cheaper way of building a mining camp than getting a traditional construction company to build apartments in the middle of nowhere for the workforce,” he says.
ATCO has been very busy the last few years working with ‘tier one’ mining companies like BHP and Rio Tinto.
“We’ve been at forefront of WA’s larger projects; we delivered housing for Chevron’s Wheatstone expansion in 2015 which was 2000 rooms and recently supplied the camp to Rio Tinto at its West Angelas operations.
“ATCO has been operating in Australia for almost 60 years, and we’re well known for doing what we do, well, and we’re always on the tender list for mining companies.”
Mr Tucker explains ATCO is a family owned global company and its first modular workers homes were made in the 1960s of timber and serviced the remote, bitterly cold Canadian oilfields. He says they still build them from timber there but in Australia the design has evolved to what is called ‘sandwich panel’ or light steel which is the preferred option. ATCO WA, he says, is the leader in light steel framing globally.
Mr Tucker explains that when ATCO came back into the West Australian market in 2010, feedback from colleagues in the mining sector was that they weren’t getting what they needed from within Australia – so they had gone offshore to find it.
“There was a lot of product coming in from Asia during the early noughties during the iron ore and gas boom. It seemed every other week there was a tender for a 2000 or 3000 workers camp and that was attracting Asian companies,” he says.
He says ATCO made a strategic decision to compete with these importers head on, using local staff and local materials.
“We concluded we would be better off creating a local, long term business to compete against the Asian providers from a volume, speed and cost effectiveness viewpoint and build up our supply chain.
“Our goal was to create a West Australian built product for a West Australian market. Yes, sure buyers can still go to China - that’s entirely up to them - but as a buyer but we want people to know they have a West Australian option. “
Demand is growing too, he says, for modular construction outside mining camps because of its speed and ease. Mr Tucker says that modern modular structures have evolved so much, it’s often difficult to tell them from an in-situ build. Customers such as schools, health and medical facilities, sports amenities, as well as tourism and lifestyle village providers are all sectors taking up the benefits a modular structure can bring.
Markets where speed of construction, minimal site disruption and ease of design and delivery are the most important and key benefits of providing modular.
To find out more contact brad.tucker@atco.com